How does spray foam insulation R-value compare?
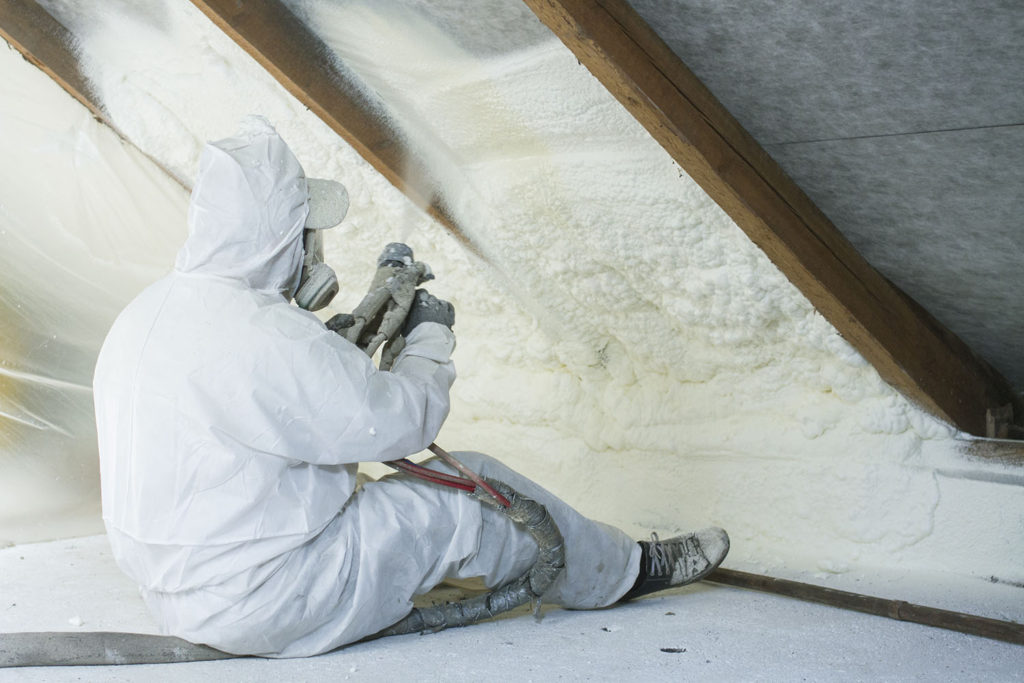
R-value, the thermal resistance measure of insulation, varies between all insulation products whether they are fiberglass, cellulose, open-cell spray foam insulation or closed-cell sprayed-in foam insulation. The higher the R-value, the greater the insulating ability.
The R-value for open-cell spray foam is between R-3.5 – R-3.6 per inch. However, there are open-cell spray foam insulation products actually offer R-3.7 per inch such as Icynene Classic and Icynene Classic Max.
In regards to closed-cell sprayed in foam insulation, R-value can range between R-4.9 to R-7.1 per inch. Closed-cell insulation products, such as Icynene ProSeal, allow builders and architects the ability to achieve R-21 in a three inch pass. Innovations such as Icynene ProSeal LE allows for an initial pass of five inches (5”) to achieve R-35.
R-Value comparison to other types of Insulation
- Fiberglass: loose – 2.2 – 2.9 R-Value per inch
- Fiberglass: batts – 2.9 – 3.8 R-Value per inch
- Cellulose – 3.1 – 3.8 R-Value per inch
- Mineral Wool: loose – 2.2 – 3.3 R-Value per inch
- Mineral Wool: batts – 3.3 – 4.2 R-Value per inch
- Cotton: batts – 3.0 – 3.7 R-Value per inch
- Spray Foam – 5.6 – 8.0 R-Value per inch
How Thick Should Spray Foam Insulation Be?
The thickness of spray foam insulation is determined by multiple factors. Insulation is rated by its R-value which measures the resistance to heat flow. A higher R-value indicates higher thermal resistance. The R-value is apparent for cellulose, fiberglass or mineral wool insulation. But the R-value of spray foam insulation depends on the type of spray foam that is installed.
The R-value of spray foam insulation is different. Spray foam insulation R-value is contingent on the type of spray foam insulation being applied. Spray foam insulation is available in open cell and closed cell.
The R-value of open cell spray foam is about 3.5 per inch, although the R-value can be different depending on the product. Open cell spray foam has a low density and is many times applied in interior walls and areas that are hard to reach in a home.
The R-value of closed cell spray foam ranges from 5.0 to 7.0 per inch, although the R-value can be different depending on the product. Closed cell spray foam is denser than open cell spray foam and is often used in areas like basement box sills where it helps prevent moisture from entering the home.
So, to answer the question “How thick should spray foam insulation be?” the answer depends on certain factors. The U.S. Department of Energy recommends insulation levels relative to the climate zone and part of the structure being insulated. It is also essential to examine the degree of moisture permeability that is needed. These factors determine whether open cell or closed cell spray foam insulation should be installed.
Understanding R-Values
Measuring a material’s R-value according to the ASTM C518 test procedure requires a heat flow meter like this German appliance manufactured by Netzsch-Gerätebau. After a sample is placed between a hot plate and a cold plate inside the calibrated testing devise, the heat flow occurring at a defined temperature difference is measured with a heat flux sensor.
R-value is a measure of a material’s resistance to heat transfer. Before 1945, resistance to heat flow was measured by referring to a material’s U-factor. The lower a material’s U-factor, the better the material is at resisting the flow of heat. Because many people assume that high numbers on a scale are “better” than low numbers, insulation manufacturers found it hard to market insulation by bragging about low U-factors. So the R-value — which is simply the inverse of U-factor — was proposed by Everett Shuman, the director of Penn State’s Building Research Institute. Since R = 1/U, the higher the R-value, the better the insulation.
Does It “Only Measure Conduction”?
Some manufacturers of radiant barriers falsely claim that R-value measures only conductive heat flow while ignoring the other two heat-flow mechanisms, convection and radiation. In fact, R-values include all three heat-transfer mechanisms.
The usual procedure for testing a material’s R-value is ASTM C518, Standard Test Method for Steady-State Thermal Transmission Properties by Means of the Heat Flow Meter Apparatus. The test method requires a technician to measure the thermal resistance of a specimen placed between a cold plate and a hot plate.
When a fiberglass batt is tested, heat flows from the hot side of the batt to the cold side. Wherever individual fibers of insulation touch each other, heat is transferred from fiber to fiber by conduction. Where fibers are separated by air, the heat is transferred from a hot fiber to a cooler fiber by radiation and by conduction through the air. Finally, the effects of any convective loops within the insulation are also captured by the test procedure.
Since a material’s R-value is the measurement of its resistance to all three heat-flow mechanisms — conduction, radiation, and convection — it is a useful way to compare insulation products.
R-Value Matters, But So Does Air Leakage
Of course, an insulated wall is affected by many factors not addressed by R-value testing. Although the R-value test captures the effects, if any, of convective loops within the insulation, it obviously cannot be expected to measure the amount of air leakage through a wall assembly once the insulation is installed. The rate of air leakage is affected by the density of the insulation, the presence or absence of an air barrier in the wall assembly, wind speed, and the stack effect.
Because of these factors, a leaky wall assembly insulated with fiberglass batts will usually perform worse than a wall assembly insulated with spray foam having the same R-value as the batts. The performance differences are due to spray foam’s ability to reduce air leakage, not to any difference in R-value between the two materials. It doesn’t make any sense to blame the R-value test for differences in air leakage between the two wall assemblies.
To obtain the best performance from fiberglass insulation, the Energy Star Homes program requires most fiberglass-insulated framing cavities to be enclosed by air barriers on all six sides. While the recommendation is sensible, it’s hard to achieve in the field. If such a six-sided air barrier can be created, however, fiberglass insulation will meet the performance expectation promised on the product’s R-value label.
Some marketers of radiant barriers or spray foam insulation imply that R-value measurements are meaningless. On the contrary, R-value is a useful measurement. But just because you know a product’s R-value doesn’t mean you know everything necessary to predict heat flow through a wall or ceiling. R-value is just one factor among many to be considered when deciding which insulation to use. Builders must also understand many other topics, including air leakage and moisture movement. No one has yet invented a “magic number” that replaces the requirement for builders to study and understand building science principles.
Does Radiant Heat Pass Through Insulation Like Radio Waves?
Another scare tactic employed by some marketers of radiant barriers is the idea that conventional insulation materials — sometimes called “mass insulation” — allow radiant heat to pass right through them. Scam artists have been known to warn builders that “mass insulation is transparent to radiant heat.” The implication is that a layer of aluminum foil is necessary to prevent radiant heat from traveling like radio waves right through a deep layer of cellulose.
In fact, most mass insulation products do a good job of stopping radiant heat flow. Radiant heat easily travels through air (for example, from a wood stove to nearby skin) or a vacuum (for example, from the sun to the earth). But radiant energy can’t travel through a solid material.
If the sun is shining on a concrete patio, for example, the heat travels to the soil below by conduction, not radiation. Here’s what happens: the concrete is first warmed by the sun (by radiation), and then the warm concrete gives off some of its heat to the ground below (by conduction). There is no radiant heat transfer from the sun to the soil.
When radiant heat hits one side of a deep layer of insulation, only a tiny percentage of that heat is “shine-through” radiation that manages to miss all of the fibers in the insulation blanket and emerge unscathed on the other side.
The fact that heat flows through a layer of insulation doesn’t mean that the insulation isn’t working. By definition, insulation slows down heat flow; it doesn’t stop it. Heat will always flow from hot to cold. The more insulation, however, the slower the heat flow.
Article by Martin Holladay, visit GreenBuildingAdvisor.com for additional blog topics.
Spray foam thermal resistance properties
Thermal resistance
R-value is the term given to thermal resistance to heat flow. The higher the R-value of an insulation product, the more effective the insulation properties. Spray polyurethane foam comes in a range of densities and cell structure. Low density foams are referred to as open cell SPF while higher density foams are referred to as closed cell foam. 1.8-2 pound polyurethane foam has the highest R-value of readily available spray foam insulation used in homes and buildings. Polyurethane is a closed-cell foam insulation material that initially contains a low-conductivity gas in its cells. As a result of the high thermal resistance of the gas, spray polyurethane insulation typically has an initial R-value around R-3.4 to R-6.7 per inch. In comparison, glass wool typically has an R-Value of only R-3 to R-4 per inch.
Foam insulation blocks all three forms of heat transfer:
Conductive heat transfer
The flow of thermal energy through a substance from a higher to a lower temperature region. Foam thermoset plastics reduce conductive heat transfer due in part to having very loose molecular bonds; In addition the cells of the installed spray foam are either filled with air in the case of open cell foam or HFC’s in closed cell foam.
Radiant heat transfer
The process by which heat energy in the form of light (usually IR unless the substrate is hot enough to glow in the visible range) is emitted more strongly by warm surfaces and absorbed by other materials especially those of low IR reflectivity (think matte black finish). Radiant heat transfer does not require a medium. Foam insulation materials, such as spray foam insulation, are opaque to thermal radiation, like most solid materials.
Convective heat transfer
Heat which is created elsewhere that is transported by means of a fluid, such as water or in our case air. Spray foam insulation’s most important attribute is the ability to air seal creating a custom airtight envelope within the building structure. The added benefit to air sealing is the ability to block convective heat transfer from interior to exterior during heating months and vice versa during cooling months, as the heat cannot escape through gaps in the buildings envelope without the aid of air movement from infiltration as a means of transport.
VOC’s Toxicity and health effects
What are volatile organic compounds (VOCs)?
Volatile organic compounds are compounds that have a high vapor pressure and low water solubility. Many VOCs are human-made chemicals that are used and produced in the manufacture of paints, pharmaceuticals, and refrigerants. VOCs typically are industrial solvents, such as trichloroethylene; fuel oxygenates, such as methyl tert-butyl ether (MTBE); or by-products produced by chlorination in water treatment, such as chloroform. VOCs are often components of petroleum fuels, hydraulic fluids, paint thinners, and dry cleaning agents. VOCs are common ground-water contaminants.
Volatile organic compounds (VOCs) are emitted as gases from certain solids or liquids. VOCs include a variety of chemicals, some of which may have short- and long-term adverse health effects. Concentrations of many VOCs are consistently higher indoors (up to ten times higher) than outdoors. VOCs are emitted by a wide array of products numbering in the thousands.
Examples include:
Paints and lacquers, paint strippers, cleaning supplies, pesticides, building materials and furnishings, office equipment such as copiers and printers, correction fluids and carbonless copy paper, graphics and craft materials including glues and adhesives, permanent markers, and photographic solutions.
Organic chemicals are widely used as ingredients in household products. Paints, varnishes, and wax all contain organic solvents, as do many cleaning, disinfecting, cosmetic, degreasing, and hobby products. Fuels are made up of organic chemicals. All of these products can release organic compounds while you are using them, and, to some degree, when they are stored.
EPA’s Total Exposure Assessment Methodology (TEAM) studies found levels of about a dozen common organic pollutants to be 2 to 5 times higher inside homes than outside, regardless of whether the homes were located in rural or highly industrial areas. Additional TEAM studies indicate that while people are using products containing organic chemicals, they can expose themselves and others to very high pollutant levels, and elevated concentrations can persist in the air long after the activity is completed.
Volatile Organic Compounds in Your Home
Volatile Organic Compounds (VOCs) are a large group of chemicals that are found in many products we use to build and maintain our homes. Once these chemicals are in our homes, they are released or “off-gas” into the indoor air we breathe. They may or may not be able to be smelled, and smelling is not a good indicator of health risk.
Common examples of VOCs that may be present in our daily lives are: benzene, ethylene glycol, formaldehyde, methylene chloride, tetrachloroethylene, toluene, xylene, and 1,3-butadiene.
Individuals can check the household product database to learn more about what’s in common household items.
Health effects of VOC exposure
The risk of health effects from inhaling any chemical depends on how much is in the air, how long and how often a person breathes it in.
Breathing in low levels of VOCs for long periods of time may increase some people’s risk of health problems. Several studies suggest that exposure to VOCs may make symptoms worse for people with asthma or who are particularly sensitive to chemicals. These are much different exposures than occupational exposures.
It is important to remember that VOCs refer to a group of chemicals. Each chemical has its own toxicity and potential for causing different health effects.
What is a safe level of VOCs?
To protect your health, it is best to limit your exposure to products and materials that contain VOCs. If you think you may be having health problems caused by VOCs, try reducing levels in your home. If symptoms persist, consult with your doctor to rule out other serious health conditions that may have similar symptoms.
Most health related studies have been conducted on single chemicals. Less is known about the health effects of exposure to combinations of chemicals. Because the toxicity of a VOC varies for each individual chemical, there is no Minnesota or federal health-based standard for VOCs as a group.
Are some people at greater risk from VOC exposure?
People with respiratory problems such as asthma, young children, the elderly and people with heightened sensitivity to chemicals may be more susceptible to irritation and illness from VOCs.
How do I reduce the levels of VOCs in my home?
First, conduct an inspection of your home for the common sources of VOCs. Look for supplies of unused chemicals, such as paints, varnishes, solvents, adhesives and caulks. Household furnishings like carpet, upholstered furniture or items made from composite wood tend to off-gas more VOCs when they are new.
Some steps to reduce your exposure include:
Source Control
Remove or reduce the number of products in your home that give off VOCs. Only buy what you need when it comes to paints, solvents, adhesive and caulks. Unused chemicals stored in the home can sometimes “leak” and release VOCs into the air. Store unused chemicals in a garage or shed where people do not spend much time.
Dispose of unused chemicals that are stored in your home or garage. Check with your city or county for housed hazardous waste collection sites. Consider purchasing low-VOC options of paints and furnishing. When buying new items, look for floor models that have been allowed to off-gas in the store. Solid wood items with low emitting finishes will contain less VOCs than items made with composite wood.
Ventilation and Climate Control
Increasing the amount of fresh air in your home will help reduce the concentration of VOCs indoors. Increase ventilation by opening doors and windows. Use fans to maximize air brought in from the outside. Keep both the temperature and relative humidity as low as possible or comfortable. Chemicals off-gas more in high temperatures and humidity. Try to perform home renovations when the house is unoccupied or during seasons that will allow you to open doors and windows to increase ventilation.
Should I test my home for VOCs?
There are no federal or state standards for VOC levels in non-industrial settings. If you are concerned about VOCs, it is best to try and reduce or eliminate the products that bring VOCs into your home.
Forum discussion
Properly installed, spray foam doesn’t pose hazards for homeowners. (Installers of spray foam need to protect themselves during their work, however.) Once cured, properly installed spray foam is not (as you assert) “quite harmful to breathe.”
That said, there can be problems when spray foam isn’t installed properly. These problems are rare but serious. To learn more about these rare situations, see Spray Foam Jobs With Lingering Odor Problems.
The second issue you raise concerns “greenness.” The main concern with closed-cell spray foam is the fact that most brands of closed-cell foam use a blowing agent that has a high global warming potential. For more information on this issue, see Avoiding the Global Warming Impact of Insulation.
A few manufacturers of closed-cell spray foam are now offering products that are made with a more benign blowing agent. If you are concerned about the global warming potential of these blowing agents — and you should be — you should use either Lapolla Foam-Lok 2000-4G or Demilec Heatlok XT HFO.
Forum discussion Response
The “soy” content of “bio-based” foams is really but a fraction of just one of the two components that are mixed, and only amount to something like 15% of the total content of the product by weight. It’s really just green-washing marketing BS. Where an application might call for closed cell foam selecting a product with a low-impact blowing agent would have far greater impact on the lifecycle environmental impact than the fraction of plant-sourced components of the polymer production.